CNC (Computer Numerical Control) machines have revolutionised parts production in advanced manufacturing. However, a complex challenge lies behind their precision and efficiency: programming these machines effectively. CAM (Computer-Aided Manufacturing) programming is a skill-intensive, time-consuming process—often the bottleneck on a busy shop floor. Addressing this global challenge is UK-based CloudNC, with its groundbreaking AI-powered solution CAM Assist.
CloudNC, a UK-based manufacturing technology company, has launched CAM Assist, an AI-driven solution to revolutionize CNC machine programming for Indian manufacturers. This initiative is facilitated through a strategic partnership with Vayam Global, a prominent software distributor in India. CAM Assist integrates seamlessly with existing CAM packages to automatically generate professional machining strategies in seconds—a task that traditionally takes programmers hours or even days. CAM Assist integrates with leading platforms like Mastercam, Fusion 360, Siemens NX, and Siemens Solid Edge.
By significantly reducing programming time, CAM Assist enhances productivity and enables manufacturers to upskill their workforce, allowing less experienced programmers to handle complex components effectively. This advancement is poised to bolster India’s manufacturing sector by improving efficiency, reducing lead times, and fostering a more skilled labor force. During a recent exclusive interview, Theo Saville, Co-Founder and CEO of CloudNC, joined Machine Maker to discuss the technology, its journey, and its immense potential for the Indian market.
Making Complex Machining Accessible: The Vision Behind CAM Assist
“The type of equipment we help control is called computer numerically controlled metal cutting robots,” Theo began. “There are millions of these deployed worldwide, with India being one of the largest markets for them.” Theo knows this firsthand—from CloudNC’s early days when they sourced components for their machinery from Indian factories. But the core problem wasn’t the availability of machines—it was the difficulty of programming them.
“Whether you’re making a wing rib, a hubcap, or a mobile phone chassis, it’s incredibly hard to find skilled labor that can program these machines,” he said. “It takes years of training.” This is true not just in the West, where manpower is scarce, but also in the East, where manpower is abundant—but skills are unevenly distributed. CAM Assist was created to change this.
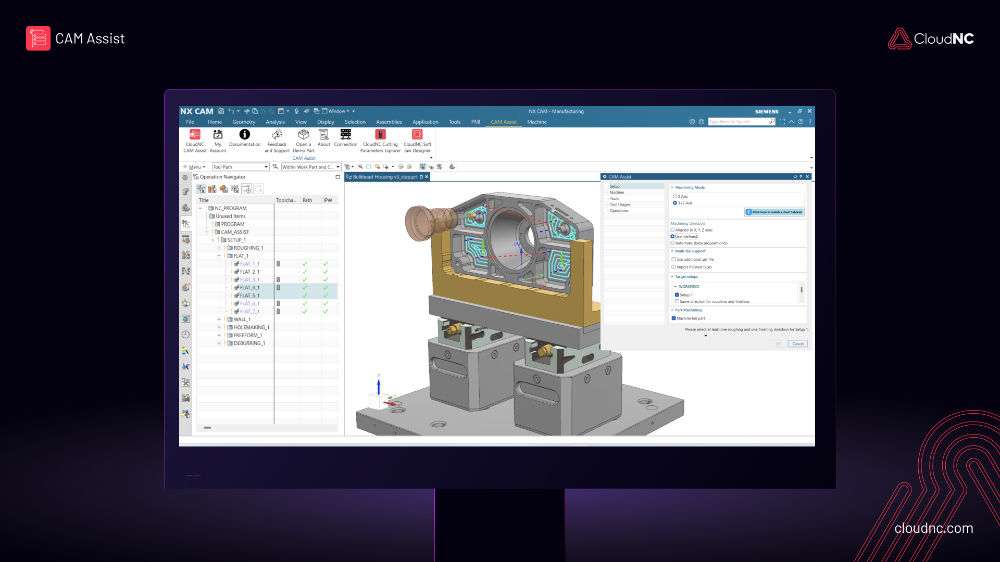
“Our software does 80% of the work,” Theo explained. “It lets users verify and fine-tune existing programs rather than creating them from scratch. And fine-tuning is always easier.”
From Frustration to Innovation: The Birth of CloudNC
The seeds of CloudNC were sown while Theo was still a university student, building a submarine with his team. Although they had a six-month deadline, manufacturing metal parts was near-impossible—lead times were 10 weeks. Used to the instant nature of 3D printing, Theo was frustrated.
“None of the CNC machines in the workshop seemed to be switched on,” he said. “When I asked if I could use them, the answer was no—they were too complicated.” That simple answer became a profound question in Theo’s mind: Why can’t someone with aptitude, even if not yet skilled, walk up and use one of these machines? That curiosity eventually became a mission.
After graduation, Theo joined a startup accelerator, met his co-founder, an expert in high-performance computing and AI, and together they began solving this problem. “It took us almost 10 years,” he said. “Not impossible, but close.”
Now, CloudNC is going global, with CAM Assist leading the way.
Bridging the Gap: Inspiring Tech Adoption in India
India is a land of contrast in the tech landscape—rapidly growing yet, in many areas, still grounded in traditional processes. Many manufacturers continue to program machines manually, accepting mistakes and inefficiencies as part of the norm. The challenge thrown to Theo was how to raise awareness about adopting technology like CAM Assist in such a landscape.
Theo’s answer was simple: “We just show them.”
Theo demonstrated how CAM Assist works. He selected a part that would typically take 8–10 hours to program by hand, even for an expert with five years of experience. He navigated the manual steps: selecting tools, setting parameters, and creating a basic toolpath. “There’s just so much opportunity to make mistakes,” he said.
Then he ran CAM Assist.
The software sent the 3D model to CloudNC’s secure servers on AWS, where it evaluated millions of toolpath strategies, optimizing each decision before returning a complete machining plan. “It’s like having someone else start the job—you just finish it.”
Human Effort Reimagined, Not Replaced
Naturally, the conversation shifted to the age-old debate about automation and jobs. As an entrepreneur, I expressed my dual perspective—excitement about the possibilities and concern for the skilled professionals whose work could be reduced. Theo responded clearly: “In our experience, there simply aren’t enough people with the skill to do this job anyway.”
He continued, “We’ve never had a customer tell us someone lost their job because of CAM Assist. We’ve seen the opposite: shops win more business, deliver faster, and expand operations.” The bottleneck in most workshops is unused machine capacity because there aren’t enough skilled programmers. CAM Assist unlocks this potential without displacing workers. “Letting people go only to hire them back later as business grows doesn’t make sense.”
For CAM Assist’s competitors, “startups are trying,” Theo admitted, “but none are moving at the pace we are.” CAM Assist today supports multi-axis, three-axis, and multi-material machining workflows. With a decade of refinement, the software is light years ahead in complexity and capability. “And yes,” he added, “we have patents—plenty.”
Integrations and Accessibility: Built to Fit, Not Replace
One of CAM Assist’s key features is its compatibility with existing CAM systems. “It’s not a standalone tool—you need a supported CAM package,” Theo explained. CAM Assist integrates with Mastercam, Fusion 360, Siemens NX, and Siemens Solid Edge. More integrations are coming, aiming to cover nearly every major CAM system over the next 18 months.
The product was officially launched in July last year, and adoption has surged globally. “We’re now in the high hundreds of users,” Theo said. “And it’s growing fast.” CAM Assist follows a cloud-based SaaS model, relying on immense computational power for real-time optimization. Pricing is customized per workshop, not per user, to keep it affordable and proportional to the value delivered. “We have great deals for individuals, small shops, and enterprises. There’s no one-size-fits-all.”
CloudNC’s team is around 90 strong, with the majority based in the UK and a growing presence in the US, which was their first international market. But India holds a special place in Theo’s roadmap. “India is very high on my list,” he said. “Sure, it’s a huge opportunity, but I’ve also spent much time here. I love the place.”
With solid reseller partnerships and a product-market fit that aligns with India’s precision manufacturing goals, CAM Assist is primed for rapid adoption.
Upskilling, Not Just Automating: A Tool for the Future
“CAM Assist makes it possible for someone with no programming background to reach the skill level of a seasoned machinist quickly,” Theo shared. “And those who already have some experience can get to expert level faster—because CAM Assist handles the routine, letting them focus on complex parts.”
He compared it to learning math: “Do you start with a pencil or a calculator? CAM Assist is like giving someone a calculator, then teaching them how to use Google Sheets.” In India—where bridging the skill gap is as important as driving productivity—CAM Assist offers a scalable, sustainable solution.
With CAM Assist, CloudNC is ushering in a smarter, more efficient, and more accessible era of CNC machining. For Indian manufacturers, this means fewer bottlenecks, more consistent output, faster deliveries, and most importantly, empowered, upskilled workers.